Jak powstaje kombajn?
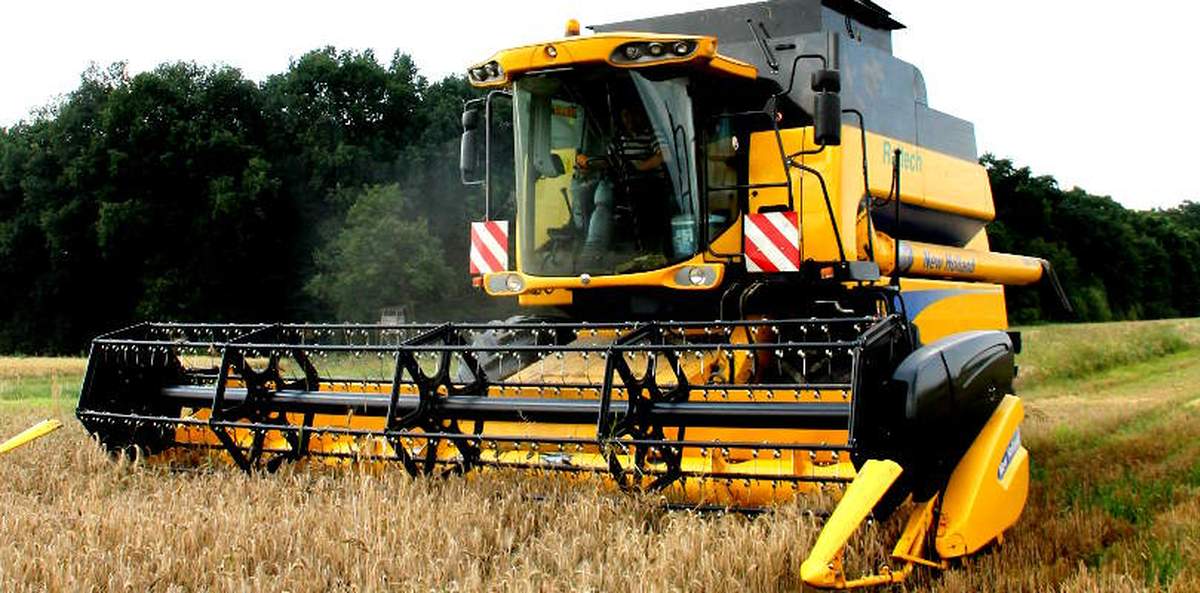
New Holland zaprosił dziennikarzy na zwiedzanie swojej fabryki w Płocku.
Dalsza część artykułu pod materiałem wideo
Hitem dni otwartych był „tańczący kombajn” z serii TC 5.90 HILL SIDE, przystosowany do zbiorów na terenach górzystych. Jest tak skonstruowany, że jedynie podwozie oraz zespół żniwny dostosowują się do ukształtowania terenu. Reszta pozostaje w poziomie.
ZOBACZ FILM Z DNI OTWARTYCH W FABRYCE NEW HOLLAND
Obecnie produkowane są tutaj kombajny zbożowe ( 10 modeli z możliwością 236 wariantów rozwiązań), prasy stało i zmiennokomorowe (16 modeli w 346 wariantach ), przyrządy żniwne (36 modeli do zbioru zbóż i rzepaku), oraz przyrządy żniwne do zbioru kukurydzy (stałe lub składane z 6 rzędami, wszystkie dzioby odchylają się dzięki zastosowaniu samonośnych amortyzatorów gazowych ułatwiających czyszczenie i konserwację ). Produkty fabryki w Płocku są wysyłane do 51 krajów na 6 kontynentach ( ok. 500 kombajnów TC rocznie odbiera Turcja). Kombajny TC uważane są za najbardziej ekonomiczne w swojej klasie (to właśnie w Płocku został wyprodukowany pięćdziesięciotysięczny kombajn tej serii!).
Kombajny CX to średni przedział maszyn do zbioru, największe kombajny to seria CR kombajny rotorowe (pierwszym tego typu kombajnem był wyprodukowany 40 lat temu kombajn TR 70), pracujące w technologii Twin Rotor (dwa rotory).
Ciekawą konstrukcję stanowi (produkowany od 10 lat) kombajn TC 5.90 HILL SIDE
Może pracować w terenie górzystym, gdyż dzięki zastosowanemu żyroskopowi może poziomować elementy robocze, przy jednoczesnym kopiowaniu przez układ jezdny ukształtowania terenu. Poziomowanie na skłonie pod górę do 30%, w dół do 10%, poprzecznie do 30%. Produkcja tych kombajnów przeznaczona jest głównie na rynek włoski.
Przedział zbioru kombajnami New Holland zawiera się od 10 do 100 ton plonu na godzinę.
Przyrządy High Capacity (otrzymują stałą wysokość ścierniska niezależnie od ukształtowania terenu dzięki płytkom nośnym i czujnikom automatycznie monitorującym położenie zespołu żniwnego), mają szerokość roboczą od 3,96 do 9,15 metra, Varifeed (zmienna odległość listwy nożowej od krawędzi podajnika ślimakowo palcowego, elektrohydrauliczna regulacja umożliwia zmianę położenia listwy tnącej z wnętrza kabiny podczas pracy) od 4,8 do 12,5 metra, przyrządy żniwne Flex (przeznaczone do zbioru soi) o szerokości roboczej od 6,05 do 10,57 metra, produkowane są również podbieracze (zbiór dwufazowy ekologicznych upraw rzepaku).
Potwierdzeniem jakości i wydajności maszyn New Holland jest ustanowiony w roku 2014 rekord świata w zbiorze ośmiogodzinnym
Został ustanowiony przez kombajn CR 10.90, wyposażony w silnik Cursor 16 o mocy 654 kM, w trakcie bicia rekordu kombajn pracował w łanie o wilgotności 16%, przy temperaturze 18 do 21ºC, przy prędkości 6 do 8 km/h zużycie paliwa wyniosło 1 litr na zebraną tonę plonu, w czasie ośmiu godzin pracy kombajn zebrał 797,656 ton!
Płock to nie tylko fabryka, ze względu na to, że stanowi centrum Europy jest również ważnym ośrodkiem badawczo rozwojowym, w którym pracują specjaliści dysponujący fachową wiedzą i doświadczeniem w dziedzinie projektowania, rozwoju produkcji oraz szkoleń związanych z maszynami żniwnymi. Szkolenia zapewniają wysoką jakość obsługi świadczonej przez lokalnych dealerów na terenie całego kraju. Maszyny New Holland tworzone według japońskiej filozofii „Kaizen”, czyli dążenia do doskonałości przez ciągły rozwój. Sprzęt oferowany na rynku to owoc doświadczeń i tradycji konstruktorów firmy.
W roku 1895 Abe Zimmerman w Pensylwanii zakłada New Holland Machine Company, w roku 1998 firma zakupuje spółkę „Bizon” w Płocku (której początek dały zakłady maszyn rolniczych M.S.Sarna powstałe w 1870 roku!). Przejęta spółka zmienia swoja nazwę na CNH Polska (w roku 2002), natomiast w roku 2014 przyjmuje obecną nazwę CNH Industrial Polska. Na wszystkich działach wdrażany jest system WCM (World Class Manufacturing), którego istotą jest to, że każdy pracownik stanowi istotną część procesu produkcji, bierze bezpośrednią odpowiedzialność za swoje działania, przeprowadza samokontrolę, w razie potrzeby dokonuje korekty oraz proponuje ulepszenia.
System oparty na ciągłym doskonaleniu umiejętności pracowniczych w sposób zorganizowany osiąganie maksymalnych korzyści poprzez ulepszanie jakości i zwiększanie bezpieczeństwa pracy. Działania pracownicze oparte na motywacji, której najważniejszym hasłem jest spełniać wymagania i oczekiwania klientów. Większość podzespołów wykorzystywanych do produkcji jest wykonywana na miejscu w Płocku, gdzie znajdują się najnowocześniejsze urządzenia do wycinania laserowego, roboty spawalnicze oraz nowoczesne systemy malowania części.
Pierwszym etapem produkcji każdej maszyny jest cięcie blach stalowych
Wycina się kształty płaskie, z których następnie wykonuje się profile poprzez gięcie odpowiednie dla danego modelu maszyny. Wydział obróbki plastycznej wykorzystuje dwa urządzenia do wycinania otworów oraz trzynaście laserów, które mogą ciąc blachy o grubości od 0,8 mm do 20 mm. Następnie poszczególne elementy trafiają do pras krawędziowych o różnym stopniu nacisku (od 100 do 320 ton.
Kolejnym etapem obróbki elementów są stanowiska spawalnicze, które wykorzystują najnowocześniejsze technologie spawalnicze.
W tym dziale znajduje się blisko 250 stanowisk do spawania manualnego i około 60 stanowisk do zgrzewania, które mogą spawać elementy o wymiarach od kilku centymetrów do kilkunastu metrów. Wszystkie elementy maszyn spawane są w specjalnych przyrządach, które pozwalają na wyeliminowanie błędów i dostarczenie do kolejnego etapu produktów najwyższej jakości. W procesie spawalniczym wykorzystywane są gazy szlachetne (np. argon), które gwarantują, że połączenia są odpowiednio wysokiej jakości i wytrzymałości.
Po spawaniu poszczególne elementy trafiają do malarni, gdzie przechodzą procesy oczyszczania, nakładania warstw podkładowych oraz warstwy lakierniczej (stosowane są metody nakładania zanurzeniowego przy wykorzystaniu zjawiska elektroforezy czyli nakładania powłok farb wodnorozpuszczalnych). Z malarni trafiają do pomieszczeń magazynowych, gdzie oczekują na przekazanie ich na odpowiednie dla nich linie montażowe. Linie montażowe pracują w systemie potokowo gniazdowym. Montowany kombajn przesuwa się wzdłuż linii montażowej (podparty na kołach mostu napędowego), zatrzymuje się na kolejnych punktach , gdzie następuje montaż kolejnych podzespołów.
Podzespoły montowane są w gniazdach montażowych, które są usytuowane prostopadle do głównej linii montażowej.
Po zmontowaniu trafiają do punktu, w którym następuje zamontowanie na właśnie montowaną maszynę. Idąc wzdłuż linii można obserwować kolejne etapy powstawania maszyny, przy zastosowaniu nowoczesnych technologii montażu, każdy element jest rejestrowany, można zawsze określić gdzie został zamontowany. Wszystkie maszyny New Holland montowane są według specyfikacji, która jest sporządzona przez rolnika i sprzedawcę. W momencie rozpoczęcia montażu danej maszyny można określić jego właściciela. Ostatnim etapem produkcji jest sprawdzenie gotowej maszyny na specjalnym stanowisku pomiarowym, na którym bada się prawidłowe działanie wszystkich podzespołów i prawidłowego działania całej maszyny.
Dopiero po przejściu szczegółowych testów maszyna może być kierowana do punktów sprzedaży.
Bardzo interesującym i ważnym stanowiskiem w odbiorze końcowym maszyny jest test CQA, podczas którego wysoko wykwalifikowani specjaliści dokonują odbioru maszyny w imieniu klienta. Z każdej partii produkcji wybierana jest maszyna, która następnie podlega szczegółowemu sprawdzeniu. Podczas testu badaniom podlega około 200 parametrów maszyny. Obecnie w Płocku montuje się dziennie siedem kombajnów (montaż jednej maszyny trwa dwa dni, gdyż musi ona przejść przez czternaście punktów montażowych), maksymalnie produkowanych jest czternaście kombajnów dziennie (wówczas czas montażu jednego kombajnu wynosi jeden dzień), Pełna produkcja kombajnów przypada na miesiące od września do kwietnia (obecnie zakład w Płocku ma zagwarantowaną produkcję kombajnów do końca czerwca!).
Wszystkie nowoczesne systemy wprowadzane w maszynach New Holland noszą nazwę „Opti...”
Układ Opti-Fan koryguje zmiany szybkości przepływu ziarna przez system czyszczący. Podczas pracy na podjazdach w górę lub zjazdach w dół zbocza prędkość wentylatora automatycznie dopasowuje się do kierunku i stopnia nachylenia, co przyczynia się do zwiększenia skuteczności czyszczenia w trudnych warunkach nawet do 30%. Wytrząsacze słomy Opti-Speed to nowoczesny system regulujący prędkość obrotową wałów wytrząsaczy w zależności od nachylenia stoku oraz od rodzaju zbieranej rośliny.
Gumowe gąsienice Smart Trax i zawieszenie Terraglide (Standardowo montowane w kombajnach CR 10.90)zapewnia powierzchnie styku z podłożem wynoszącą nawet 1,4 m², co przekłada się na zwiększoną stabilność jazdy oraz zapewnia optymalne właściwości jezdne na najbardziej grząskim terenie, ubijanie gleby zmniejszono o 57% w porównaniu z maszynami kołowymi. Zwiększenie długości gąsienic poprawia przyczepność, dwie pary wałków na zawieszeniu hydraulicznym działają niezależnie gwarantując bardzo płynna jazdę. Automatyczny system Intellicruise optymalizuje prędkość jazdy w zależności od przepustowości, tak aby zagwarantować najwyższą wydajność, niezależnie od zmieniających się warunków zbioru.
Układ czyszczący Triple-Clean dzięki zastosowaniu dodatkowej kaskady umieszczonej w centralnej części podsiewacza zwiększył wydajność oczyszczania o około 15%.
Nowa kabina Harvest Suite Comfort zawieszona jest na wibroizolatorach tłumiących drgania, poziom hałasu wynosi w jej wnętrzu 74 dB, widoczność to przeszklona powierzchnia 6,3 m², przestrzeń wnętrza to 3,7 m³. Dostępny opcjonalnie fotel z amortyzacja pneumatyczną dostosowuje się do potrzeb operatora. W kabinie operator ma dostęp do kluczowych informacji dzięki monitorowi InfoView II, który wyświetla tylko niezbędne informacje, pomijając informacje o mniejszym znaczeniu. Płock to (nieprzerwanie od końca dziewiętnastego wieku ) ważny ośrodek produkcji maszyn rolniczych w Polsce, obecnie zakłady zatrudniają około 1400 osób (w okresach wzmożonej produkcji zatrudnienie osiąga poziom około 2000 ludzi), zdecydowana większość to pracownicy fizyczni (pracowników umysłowych jest zatrudnionych 110). Płocki producent kombajnów, nie tylko zatrudnia, ale również regularnie płaci podatki do budżetu naszego państwa!